Busting the Myths of Welding of High Strength S690 and S960 Steel
Adverse effects of welding on high strength steel have always been a concern of construction engineers and remain a commonly asked question in the application of S690 and S960 in construction. CNERC has conducted a comprehensive series of tests on the S690 welded sections and structural members, including microstructural evolution within heat affected zones of welded sections, mechanical properties, and structural behaviour. The welding technology for high strength S690 steel and complementary certified welding procedure specifications were also critically reviewed.
Results indicate that with proper welding procedures, appropriate welding electrodes and good temperature control, structural performance of S690 welded sections is similar to those of S355 and S460 steel. Understanding the welding effects is key to the comprehension of structural performance of high strength S690 and S960 steel structures, and it can unlock full potentials and wide applications of these steel in construction.
In many modern steel mills, these high strength steel are manufactured with a highly controlled heat treatment process known as “Quenching and Tempering” to produce a homogeneous microstructure of tempered martensite. This is a fine-grained crystalline form of steel with high strengths and toughness. However, a transient heating / cooling cycle induced during welding of these steel may initiate phase transformation, re-crystallisation and grain growth, i.e. to transform into a heterogeneous microstructure, within the heat affected zones of the welded joints, as shown in Fig. A.
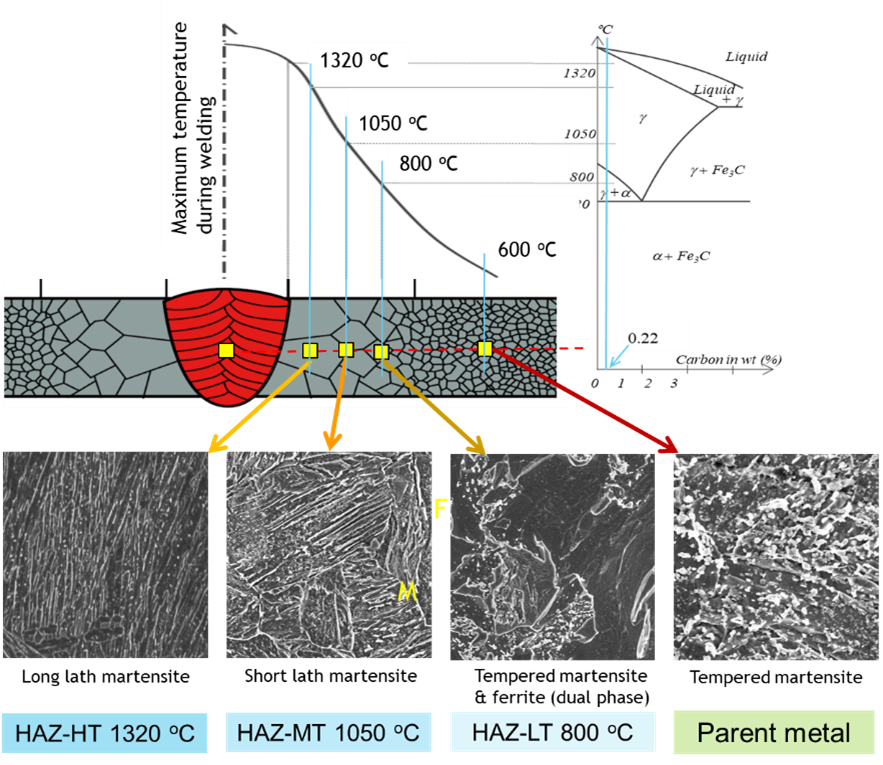
It is important to control the heating up as well as the cooling down processes so that any microstructural change in the heat affected zones of the welded joints is kept to be a minimum. This is generally achieved through a careful selection of various welding parameters according to geometrical details of the weld joints so that the heat input energy during welding is kept to be a practical minimum. Then, the welded joints are cool down quickly, giving little time for a significant microstructural change to take place within the heat affected zones. In general, the time for the steel to cool down from 800 oC to 500 oC, i.e. t8/5 , is often adopted for this purpose. In practice, the value of t8/5 should not exceed 10 to 15 seconds in those steel plates of 10 to 50 mm thick.
Hence, welding in these steel will potentially cause a significant reduction in their mechanical properties if both the maximum temperatures during welding and the cooling rates after welding are not properly controlled, in particular, in those steel plates with practical thicknesses in construction, i.e. 6 to 80 mm thick. It is highly desirable to assess or predict reductions in various mechanical properties of these welded sections, and more importantly, how to eliminate any such reduction in these welded sections.