Game-changing discovery: power of 3D printing to create titanium alloy
Other Articles
Titanium alloys are advanced lightweight materials indispensable for many critical applications. In a groundbreaking discovery, researchers from PolyU in collaboration with RMIT University and the University of Sydney have developed high-performance titanium alloy using 3D printing technology. The research was published in Nature, a leading international weekly journal of science first published in 1869. The research could help extend the applications of titanium alloys, foster sustainability and drive innovative materials technologies.
Existing challenges
While traditional manufacturing methods, such as casting, can be used to produce titanium alloy, the poor properties of the resulting material may render it unsuitable for practical engineering.
Also, the energy-intensive Kroll process, typically used to produce titanium alloys, generates off-grade sponge titanium, which accounts for approximately 10% of all sponge titanium, resulting in substantial waste and increased production costs.
Overcoming limitations
Instead, the research team has successfully used additive manufacturing, also known as 3D printing, to solve those long-standing issues in titanium alloy production. Through the use of 3D printing, the research team has produced a new strong, ductile, and sustainable titanium alloy (α–β Ti-O-Fe alloy). These properties are achieved by incorporating inexpensive and abundant oxygen and iron, the two most powerful stabilising elements and strengtheners for α–β phase titanium alloys.
The team resorted to additive manufacturing for the production of titanium alloys.
Additionally, it can be used to fabricate metal parts with unique structures and compositions, which cannot be achieved using traditional methods.
3D printing can also effectively address the challenges associated with quality and waste by enabling the recycling of off-grade sponge titanium, converting the waste into powder for use as raw material.
Expanding applicability
The research team’s discovery of the innovative use of additive manufacturing to produce titanium alloys and potentially other metal materials offers numerous advantages, such as reduced costs, improved performance, and sustainable waste management.
Compared with the Ti-6AI-4V benchmark material, which has been widely used since its formulation in 1954, the new titanium alloy produced by the research team demonstrates better mechanical performance, with comparable ductility and considerably higher strength.
The new titanium alloy has immense potential for diverse applications, in areas from aerospace, marine engineering, consumer electronics to biomedical devices, thanks to its enhanced strength, flexibility, and cost-effectiveness.
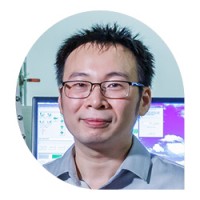
Our work can facilitate the recycling of more than 10% of waste generated by the metal alloy production industry. This can significantly lower both material and energy costs for industries, and contribute to environmental sustainability and carbon footprint reduction.
~ Dr Zibin Chen
PolyU’s U3DP listed among global top university 3D printing labs 2022 |
![]() |
The University Research Facility in 3D Printing (U3DP) has been named one of the Top University 3D Printing Labs of 2022 in the world by All3DP, a leading Munich-based magazine for digital makers. Established in 2017, U3DP represents another major step taken by the University to enhance and promote the culture and environment within which research can thrive and excel. It is the first and only one of its kind among Hong Kong higher education institutions, the city’s largest research centre in 3D printing in terms of range and quantity of facilities, and also houses the very first Makerbot Innovation Centre in the Asia Pacific region. |